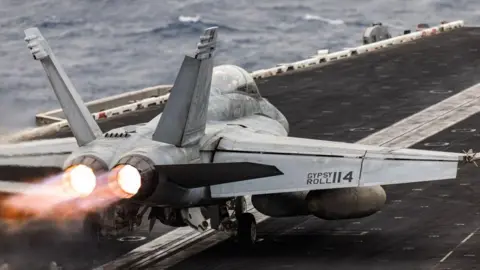
Düsentriebwerke sind eine der atemberaubendsten technischen Leistungen, die Menschen jemals hervorgebracht haben.
Aber Düsentriebwerke sollten nicht möglich sein, sagt Ben Beake, Leiter der Materialforschung bei Micro Materials, einem Gerätetestunternehmen in Wales.
„Die einströmende Luft ist heißer als der Schmelzpunkt des darunter liegenden Metalls – was natürlich nicht gut ist“, erklärt er und weist darauf hin, dass diese Luft Temperaturen deutlich über 1.000 °C erreicht.
Entwickler von Strahltriebwerken haben dieses Problem durch die Anwendung umgangen hitzebeständige Keramikbeschichtungen zu den Triebwerksschaufeln. Und jetzt entwickeln Forscher noch stärkere Beschichtungen, die es den Motoren ermöglichen, noch heißer zu laufen.
„Wenn es heißer wird, können enorme Kraftstoff- und CO2-Einsparungen erzielt werden“, sagt Dr. Beake. Er schätzt, dass eine Erhöhung der Temperatur um nur etwa 30 °C zu einer Kraftstoffeinsparung von 8 % führen könnte.
Das ist die Kraft von Beschichtungen – sie verändern die Funktionalität und Fähigkeiten eines darunter liegenden Materials radikal. Nur wenige Menschen wissen, wie wichtig sie sind, aber diese Overlays und Furniere können Hochleistungsmaschinen aufladen oder dafür sorgen, dass teure Geräte den härtesten Umgebungsbedingungen standhalten.
Dr. Beake und seine Kollegen haben die Aufgabe, Beschichtungen an ihre Grenzen zu bringen, um herauszufinden, wie robust und effektiv sie wirklich sind. Seine Kunden erzielen nicht immer die gewünschten Ergebnisse. Er erinnert sich, wie er vor einigen Jahren einem Raketenhersteller sagte: „Wir haben Ihre Beschichtung zerstört“. „Sie stürmten verärgert davon“, sagt Dr. Beake.
Micro Materials setzt Beschichtungen nicht nur hohen Temperaturen aus, sondern verfügt auch über ein „Specht“-Gerät, einen winzigen Diamantstift, der wiederholt an zufälligen Stellen auf eine Beschichtung klopft, um deren Haltbarkeit zu testen.
Kürzlich hat das Unternehmen mit dem in Großbritannien ansässigen Unternehmen Teer Coatings zusammengearbeitet, um ein Produkt zu testen, das auf Satellitenkomponenten angewendet werden kann, darunter Zahnräder und Lager, die in verschiedenen beweglichen Teilen verwendet werden.
Eine knifflige Aufgabe, sagt Xiaoling Zhang vom Unternehmen, denn die Beschichtung müsse solche Komponenten sowohl vor dem Start (wenn sie der Luftfeuchtigkeit am Boden ausgesetzt sind) als auch im Orbit vor Staubpartikeln und Strahlung im Weltraum schützen. Sie behauptet jedoch, dass das Unternehmen die gewünschten Ergebnisse erzielt habe.
Doch Beschichtungen schützen nicht nur Raumfahrzeuge, sondern könnten auch verhindern, dass Astronauten erkranken.
Biofilme – klebrige Ansammlungen von Bakterien in Rohren – wachsen in Umgebungen mit geringer Schwerkraft schnellerDies könnte zum Beispiel ein Problem für die Wasserversorgung oder Maschinen sein, die Flüssigkeiten auf Raumstationen oder zukünftigen Raumfahrzeugen bewegen.
„Biofilme verursachen bekanntermaßen mechanische Ausfälle“, sagt Kripa Varanasi vom Massachusetts Institute of Technology. „Das willst du nicht.“
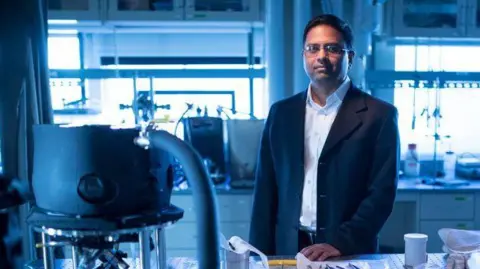
Prof. Varanasi und seine Kollegen haben eine Reihe von Beschichtungen entwickelt, die Oberflächen rutschig und damit resistent gegen die Bildung von Biofilmen machen. Tests einer solchen Beschichtung in einem an Bord der Internationalen Raumstation durchgeführten Experiment ergaben, dass dies der Fall ist hat wie vorgesehen funktioniert.
Die Idee hinter der Beschichtung besteht darin, einen festen Stoff und einen Schmierstoff miteinander zu vermischen. Dieses wird dann auf die Innenseite eines Rohrs oder einer Röhre gesprüht, wodurch die Innenfläche extrem rutschig wird.
Prof. Varanasi hat bereits mit der Entwicklung ähnlicher Beschichtungen für Schlagzeilen gesorgt die Innenseiten von Zahnpastapackungen – damit Sie auch das letzte bisschen Zahnpasta herausbekommen. Er und seine Kollegen haben die Technologie über ihr Spin-out-Unternehmen LiquiGlide kommerzialisiert.
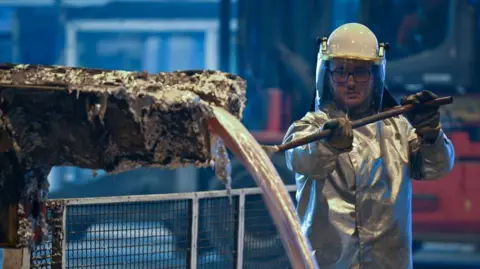
Rutschigkeit ist vielleicht eine unterschätzte Eigenschaft. Nuria Espallargas von der norwegischen Universität für Wissenschaft und Technologie und Kollegen haben eine Beschichtung auf Siliziumkarbidbasis für Geräte entwickelt, die bei der Aluminiumherstellung oder -reparatur verwendet werden.
Es handelt sich um eine Art antihaftbeschichtete Bratpfannenlösung, was bedeutet, dass Schichten geschmolzenen Aluminiums nicht an diesem teuren Gerät haften bleiben. Die genaue Funktionsweise dieser speziellen Beschichtung ist derzeit allerdings noch ein Rätsel.
„Um ehrlich zu sein, wissen wir wirklich nicht, wie es funktioniert, der Mechanismus ist derzeit unbekannt“, sagt Prof. Espallargas.
Dennoch ist die Beschichtung über ihre Spin-out-Firma Seram Coatings kommerziell erhältlich. Atlas Machine and Supply, ein US-Unternehmen, das Industriemaschinen herstellt und repariert, hat es ausprobiert.
„Der eigentliche Vorteil liegt in der Verlängerung der Lebensdauer der Werkzeuge und der Verbesserung der Qualität der hergestellten Produkte“, sagt Jeremy Rydberg, Chief Innovation Officer.
Er sagt, dass Atlas ohne die Beschichtung die Walzenwerkzeuge, mit denen es Aluminium bearbeitet, alle zwei Tage neu aufbauen muss. Dies kostet jährlich 4,5 Millionen US-Dollar. Aber die neue Beschichtung bedeutet, dass diese Werkzeuge eine ganze Woche und nicht nur ein paar Tage halten, was die Wiederaufbaukosten auf etwa 1,3 Millionen US-Dollar pro Jahr senkt.

Beschichtungen können erstaunliche Dinge bewirken, aber sie funktionieren nicht immer wie vorgesehen, bemerkt Andy Hopkinson, Geschäftsführer der Safinah Group, einer Firma, die häufig mit Untersuchungen beauftragt wird, wenn Beschichtungen schiefgehen.
„Wir sehen im Moment viele Probleme bei Parkplätzen, wo ihr passives Brandschutzsystem abblättert“, sagt er und bezieht sich auf die feuerbeständige Farbe, die manchmal auf Betonkonstruktionen aufgetragen wird.
Und sein Unternehmen hat auch herausgefunden, dass Beschichtungen auf Handelsschiffen nicht immer verhindern, dass sich Seepocken und andere Meereslebewesen am Rumpf festsetzen. Dieses als Biofouling bekannte Problem erhöht die Reibung, also die des Schiffes Der Motor muss mehr arbeiten – und mehr Kraftstoff verbrennen.
Trotz der Verfügbarkeit versprechender Beschichtungen entscheiden sich Schiffseigner nicht immer für die richtige Beschichtung für ihr Schiff. Diese Wahl sollte davon abhängen, wohin das Schiff fährt, wie lange es im Leerlauf statt in Bewegung sein soll usw., sagt Dr. Hopkinson.
Die Kosten für die Behebung solcher Probleme können mehrere tausend oder sogar Millionen Pfund betragen. „Normalerweise betragen die Kosten für Farbe zwischen 1 und 2 % des Projekts. Das Problem ist, dass die Kosten exponentiell steigen, wenn etwas schiefgeht“, sagt Hopkinson.
Die auf diesem Gebiet tätigen Forscher sagen jedoch, dass es noch viele Möglichkeiten gibt, Beschichtungen zu verbessern und neue zu entwickeln, die die Leistung von Maschinen oder Infrastruktur in Zukunft drastisch verbessern könnten.